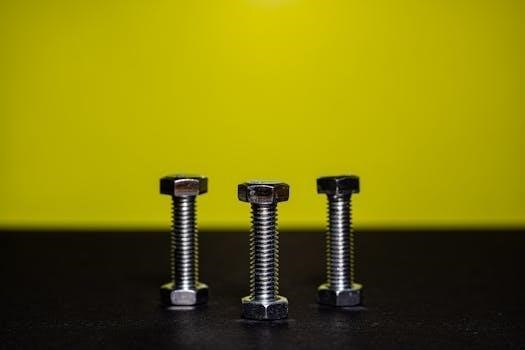
-
By:
- elizabeth
- No comment
stainless steel bolt tightening torque chart pdf
Stainless Steel Bolt Tightening Torque Chart PDF⁚ A Comprehensive Guide
This comprehensive guide will explore the crucial aspects of stainless steel bolt tightening torque, providing information for engineers, technicians, and DIY enthusiasts. It delivers valuable insights into achieving secure and reliable connections using stainless steel fasteners. Also, it helps prevent failures in various applications.
Stainless steel bolts are essential components in numerous industries, prized for their corrosion resistance, durability, and strength. These fasteners are commonly used in environments where exposure to moisture, chemicals, or extreme temperatures is prevalent. Understanding the properties and proper usage of stainless steel bolts is critical for ensuring structural integrity and preventing failures.
Torque, in the context of fasteners, refers to the rotational force applied when tightening a bolt. Applying the correct torque is paramount for achieving the desired clamp load, which is the force that holds the connected parts together. Insufficient torque can lead to loosening and joint failure, while excessive torque can cause bolt yielding or breakage. Therefore, accurately determining and applying the appropriate torque value is crucial for the reliability and longevity of any bolted joint. This guide provides essential information on the properties and applications of stainless steel bolts and torque.
Understanding Torque and its Importance in Fastening
Torque, in the realm of fastening, represents the rotational force applied when tightening a bolt or screw. It’s not merely about how tightly you can twist a fastener, but rather about achieving the precise level of tension required to clamp materials together securely. This tension, known as clamp load, is the fundamental force that prevents joints from separating under stress. Understanding torque is vital for ensuring the integrity and reliability of any mechanical assembly.
The significance of torque in fastening cannot be overstated. Applying insufficient torque results in a loose joint, prone to vibration, fatigue, and eventual failure. Conversely, excessive torque can damage the fastener, strip threads, or even cause the bolt to break. Both scenarios compromise the joint’s structural integrity and can lead to catastrophic consequences, especially in critical applications. Therefore, mastering the concept of torque and its proper application is paramount for engineers, technicians, and anyone involved in mechanical assembly.
Factors Affecting Torque Values for Stainless Steel Bolts
Several factors influence the appropriate torque values for stainless steel bolts. These factors must be considered to ensure accurate tightening and prevent joint failure. The bolt’s size and diameter are primary determinants. Larger bolts generally require higher torque values to achieve the necessary clamp load. Thread pitch also plays a role, with finer threads typically requiring slightly higher torque than coarser threads of the same diameter.
The material properties of the stainless steel itself are significant. Different grades of stainless steel possess varying tensile strengths, affecting the torque required to reach the desired tension. Surface conditions, including the presence of lubrication or coatings, drastically alter friction between the threads. Lubrication reduces friction, allowing for a higher clamp load at a given torque. Conversely, dry or corroded threads increase friction, necessitating higher torque to achieve the same clamp load. The type of lubricant used also matters, with some lubricants being more effective than others.
Common Stainless Steel Grades and Their Torque Specifications
Different stainless steel grades exhibit varying mechanical properties, directly impacting torque specifications. Two of the most common grades are 304 (A2) and 316 (A4) stainless steel. Grade 304 is a general-purpose stainless steel known for its corrosion resistance and weldability. Grade 316 offers enhanced corrosion resistance, particularly against chlorides, making it suitable for marine and chemical applications.
Due to its higher alloy content, 316 stainless steel generally has slightly different torque requirements compared to 304. When consulting torque charts, it’s crucial to differentiate between these grades. The specific torque values will depend on the bolt size, thread pitch, and lubrication conditions. However, a baseline understanding of the differences between these grades is essential for selecting the appropriate torque specifications.
Other stainless steel grades, such as 410 and 430, are also used in fastener applications, although less frequently than 304 and 316. Always refer to the manufacturer’s specifications or reliable torque charts that specify the stainless steel grade to ensure proper tightening.
Recommended Tightening Torque Chart for Stainless Steel Bolts (ASTM F593 & F837)
When working with stainless steel bolts conforming to ASTM F593 (for hex head cap screws) and ASTM F837 (for socket head cap screws), it’s essential to consult a reliable tightening torque chart. These standards define the mechanical properties and dimensions of the bolts, and the torque chart provides recommended values for achieving the correct clamp load without damaging the fastener or joint. The chart typically specifies torque values based on bolt size, thread pitch, and lubrication conditions.
A typical torque chart will present a matrix of bolt sizes (e.g., 1/4-20, 3/8-16, M6, M8) and corresponding torque values in units such as foot-pounds (ft-lb) or Newton-meters (N-m). Some charts may also include separate columns for dry and lubricated conditions. When using a torque chart, carefully identify the bolt size, grade, and thread pitch. If lubrication is used, ensure that the chart provides values for lubricated conditions.
It’s crucial to understand that the values in the torque chart are guidelines, and actual torque requirements may vary based on specific application conditions. However, the chart serves as a valuable starting point for achieving proper tightening. Always verify the chart’s source and ensure that it aligns with the relevant ASTM standards for stainless steel bolts.
Lubrication Effects on Stainless Steel Bolt Torque
Lubrication plays a crucial role in achieving accurate and consistent tightening of stainless steel bolts. Applying a lubricant to the threads and bearing surfaces reduces friction during tightening, leading to a more predictable relationship between torque and clamp load. Without lubrication, stainless steel fasteners are prone to galling, which can cause seizing and prevent the bolt from reaching the desired tension.
When using a torque chart, it’s essential to consider the lubrication conditions specified in the chart. Torque values for dry and lubricated conditions can differ significantly. Using a dry torque value on a lubricated fastener can lead to over-tightening and potential damage, while using a lubricated torque value on a dry fastener can result in under-tightening and a loose joint.
The type of lubricant used can also affect the torque-tension relationship. Molybdenum disulfide (MoS2) lubricants are commonly recommended for stainless steel fasteners due to their high load-carrying capacity and ability to reduce friction. Other suitable lubricants include anti-seize compounds and thread lubricants specifically designed for stainless steel. Always follow the lubricant manufacturer’s recommendations for application and compatibility.
It is very important to remember that lubricated values were calculated at 90 of the dry condition test results.
Performing Torque-to-Failure Tests for Accurate Torque Determination
While torque charts provide valuable guidelines, conducting torque-to-failure tests offers a more precise method for determining appropriate torque values for specific applications using stainless steel bolts. This involves gradually increasing the applied torque until the fastener fails, providing data on the maximum torque the bolt can withstand under actual operating conditions.
To perform a torque-to-failure test, construct at least ten assemblies of the application joint. Use a calibrated torque wrench to tighten the bolts or machine screws in each assembly. Incrementally increase the torque, recording the torque value at which failure occurs. Failure can manifest as stripping of threads, yielding of the bolt, or fracture of the fastener.
Analyze the data collected from the tests to determine the average failure torque. Apply a safety factor to this value to establish the recommended tightening torque. A common safety factor is 75% of the average failure torque.
This method accounts for variations in materials, manufacturing processes, and application-specific factors, resulting in a more accurate and reliable torque specification. Moreover, torque-to-failure testing ensures that you are not overtightening or undertightening the joints.
Document all test procedures, data, and calculations for future reference and quality control purposes.
Avoiding Galling in Stainless Steel Fasteners
Galling, also known as cold welding, is a common issue with stainless steel fasteners, particularly during tightening. It occurs when friction between the mating threads generates heat, causing the surfaces to seize and lock together, potentially leading to thread damage or fastener failure. Preventing galling is crucial for maintaining the integrity of stainless steel bolted joints.
One of the most effective ways to avoid galling is through proper lubrication. Applying a suitable lubricant, such as molybdenum disulfide (MoS2) or a specialized anti-galling compound, reduces friction and prevents the threads from seizing. Ensure the lubricant is compatible with stainless steel to avoid corrosion issues.
Control the speed of tightening. High-speed tightening, especially with impact drivers, generates more heat and increases the risk of galling. Use a slow and steady tightening speed to minimize heat buildup.
Using fasteners with rolled threads instead of cut threads can also mitigate galling. Rolled threads are smoother and have a work-hardened surface, reducing friction. Consider using dissimilar stainless steel grades for the bolt and nut. Different alloys have different hardness levels which reduces friction.
Proper installation practices, combined with appropriate materials and lubricants, significantly reduce the likelihood of galling, ensuring reliable and long-lasting stainless steel fastener performance.
Metric vs. Imperial Torque Values for Stainless Steel Bolts
When working with stainless steel bolts, it’s crucial to understand the distinction between metric and imperial (or US customary) torque values. Metric measurements, such as Newton-meters (Nm), are based on the International System of Units (SI), while imperial measurements, such as foot-pounds (ft-lbs) or inch-pounds (in-lbs), are commonly used in the United States.
Torque charts typically provide values in both metric and imperial units to accommodate different user preferences and equipment. Always ensure you are using the correct unit of measurement for your torque wrench to avoid over- or under-tightening the bolts.
Converting between metric and imperial torque values requires specific conversion factors. For example, 1 foot-pound is equal to 1.356 Newton-meters, and 1 inch-pound is equal to 0.113 Newton-meters. Using online calculators or conversion tables can help accurately convert between these units.
It’s also important to note that bolt sizes are different between metric and imperial systems. Metric bolts are designated by “M” followed by the diameter in millimeters (e.g., M8, M10), while imperial bolts are specified by their nominal diameter in inches (e.g., 1/4 inch, 3/8 inch). Using the correct size designation is crucial when consulting torque charts.
Always double-check the units and bolt sizes to ensure accurate torque application, which prevents fastener failure and maintains joint integrity.
Using Torque Wrenches for Accurate Tightening
Using torque wrenches is essential for achieving accurate tightening of stainless steel bolts. These specialized tools apply a specific amount of torque, preventing over-tightening and under-tightening, both of which can lead to joint failure. There are several types of torque wrenches, including click-type, beam-type, and digital torque wrenches, each with its advantages.
Click-type torque wrenches are the most common, providing an audible “click” when the desired torque is reached. Beam-type wrenches use a pointer that indicates the torque value on a scale. Digital torque wrenches offer precise readings on a digital display and often include features like data logging.
Before using a torque wrench, ensure it is properly calibrated. Calibration verifies the accuracy of the wrench and should be performed regularly, especially in critical applications. Calibration services are available from specialized companies, or some advanced digital wrenches may offer self-calibration features.
When tightening a bolt, apply the torque slowly and smoothly to avoid exceeding the target value. Ensure the bolt threads are clean and lubricated, as lubrication can affect the torque required. Always follow the manufacturer’s instructions for the specific torque wrench being used.
Using a torque wrench correctly ensures that stainless steel bolts are tightened to the correct specifications, providing secure and reliable connections in any application. It is important to always double check units of measurement.
Resources for Stainless Steel Bolt Torque Charts and Specifications
Finding reliable resources for stainless steel bolt torque charts and specifications is crucial for ensuring proper assembly and joint integrity. Several resources can provide the necessary data, including manufacturer catalogs, industry standards organizations, and online databases.
Manufacturers of stainless steel bolts often provide detailed torque charts and specifications for their products. These charts typically include recommended torque values for various bolt sizes, grades, and lubrication conditions. Consulting the manufacturer’s documentation is always a good starting point.
Industry standards organizations such as ASTM International and ISO offer comprehensive standards that include torque specifications for stainless steel fasteners. These standards provide detailed information on testing methods, material properties, and recommended torque values.
Online databases and engineering resources can also be valuable sources of torque charts and specifications. Websites dedicated to fastener information often compile data from various sources, providing a convenient way to search for the required information. However, it’s essential to verify the accuracy of the data from these sources.
When using any torque chart or specification, it is crucial to consider the specific application and operating conditions. Factors such as temperature, vibration, and the presence of corrosive substances can affect the required torque. Always consult with a qualified engineer or fastener expert if you have any doubts about the appropriate torque value.